Les solutions anti-usure réduisent les temps d'arrêt et augmente l’efficacité énergétique des papeteries
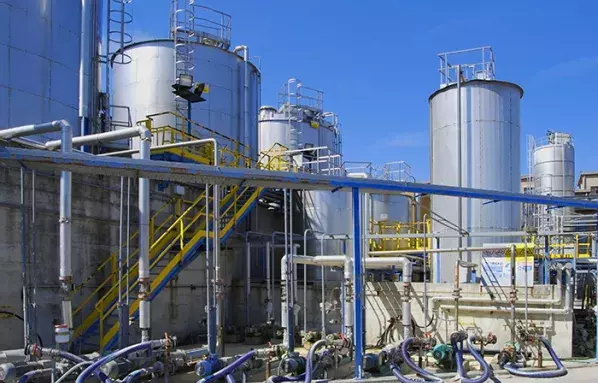
L'usure des composants vitaux des machines constitue un problème important pour l'industrie de la pâte à papier et du papier. Elle entraîne des coûts supplémentaires liés aux réparations, le remplacement et la maintenance continue, ainsi que des coûts des pertes de production.
Les équipements de fabrication de la pâte et du papier sont soumis à différents types d'usures tels que l'abrasion, le choc, l'érosion, la fatigue, la corrosion, la haute température et leurs combinaisons. Depuis 1906, Castolin Eutectic développe et applique des solutions anti-usure innovantes pour toutes le phase des processus de fabrication, depuis la cour à bois jusqu'aux services de l'usine. Cette approche fait partie intégrante de cette philosophie pionnière de la durabilité industrielle, lorsque les équipements critiques fonctionnent de manière optimale la consommation énergétique est moindre. Par conséquent, la protection contre l'usure peut non seulement aider les opérateurs des papeteries à accroître leur productivité, mais aussi à améliorer leur efficacité énergétique et à réduire leur empreinte CO2.
Cet article présente les avantages pratiques de la protection contre l'usure dans les processus clés tout au long du processus de production de la pâte et du papier.
Système de convoyeur de bois
Les pignons de la chaîne de convoyage sont des éléments clé du système de convoyage dans les parcs à bois. Les dents du pignon sont soumises à des niveaux élevés d'usure par l'écorce détachée, les encrassements et le sable. Les temps d'arrêt du convoyeur sont très coûteux car la production de copeaux est stoppée. En renforçant les dents avec deux couches différentes de fil de soudure, une couche de base sélectionnée pour sa résistance aux impacts tandis que la couche supérieure offre une résistance à l'abrasion, l'usure sera considérablement réduite. Toutefois, il est important de veiller à ce que le rechargement soit plus tendre que la chaîne pour éviter l'usure prématurée de celle-ci. Cette solution peut prolonger de 200 % la durée de vie de ces pignons.
Les maillons de la chaîne eux-mêmes s'usent sur le dessus à cause de l'abrasion, ce qui provoque le glissement des billets sur le convoyeur. C'est bien pire en hiver lorsqu'il y a du gel et de la glace sur les grumes. On peut remédier à ce problème en revêtant chaque maillon d'un alliage fusible qui contient des grains de carbure de tungstène de taille grossière avec de la poudre d’un alliage base nickel. En résultat est obtenu un revêtement dur et résistant à l'usure qui est idéal lorsqu'une surface antidérapante est requise. Cette solution est connue pour durer plus de cinq ans sans aucun signe d'usure ou de manque de traction.
Déchiquetage écorce
Les industries du bois et du papier utilisent l'écorce et les déchets de bois issus de l'écorçage de plusieurs façons. Les scieries utilisent ce matériau comme combustible pour produire de la vapeur d’eau afin de faire fonctionner des séchoirs pour sécher le bois vert. D'autres mettent en place des usines de paillage d'écorce pour traiter et emballer les déchets afin de les utiliser pour l'horticulture ainsi que comme matériau de remplissage dans les panneaux de construction. Les papeteries traitent l'écorce et l'utilisent dans des chaudières à écorce pour produire la vapeur pour l'usine. La préparation de l'écorce utilise des marteaux, des convoyeurs, des vis d'alimentation et des ventilateurs. Tous ces équipements sont soumis à l'usure due à l'action abrasive de l'écorce et des déchets de bois.
Certains sites utilisent des broyeurs à griffes, où les pointes des marteaux subissent la majeure partie de l'usure due à l’abrasion de l'écorce du bois. Les matières étrangères comme les clous, les fils métalliques, etc. provoquent une usure supplémentaire. Reconstruire les pointes par soudage et un revêtement en poudre fusionnée peut augmenter la durée de vie des pointes de plus de 100 %.
D'autres installations équipées de broyeurs d'écorce connaissent une usure rapide de la bande d'éjection installée à la sortie. Son usure rapide se fait suite à la forte abrasion et l'érosion. Dans un cas, le remplacement de la plaque d'origine fabriquée en acier résistant à l'usure par une solution CDP® (CastoDur Diamond Plate) à base de matériaux composites bimétalliques a permis d'augmenter la durée de vie de 200 %.
Transfert des copeaux et cyclones
Dans les broyeurs, les copeaux sont généralement transportés par voie pneumatique dans des tuyaux ou sur des bandes transporteuses. D'autres systèmes tels que les convoyeurs à chaîne et à vis sont également utilisés pour déplacer les copeaux, mais généralement sur des distances relativement courtes.
Dans un cas, une forte érosion a été constatée sur un tube de levage situé à la sortie du broyeur vers le cyclone. Bien que de l'acier résistant à l'usure ait été utilisé, un client avait constaté que l'unité s'était brisée prématurément. Un remplacement a été fabriqué à partir du neuf en utilisant une plaque d'usure CDP. Les bords latéraux extérieurs ont été renforcés par un profilé en fer et soudés avec un fil spécialement sélectionné. Les joints de soudure internes ont également été renforcés avec du fil de rechargement. Le résultat a été une augmentation de 400% de la durée de vie.
Les rotors de ventilateur souffrent également d'une usure érosive importante due au mélange de bois, de sable et de poussière dans le flux d'air. Cela entraîne un temps d'arrêt coûteux pour chaque réparation, car il faut le démonter avec une grue. Pour une réparation, où l'usure s'est avérée très localisée, des bandes de plaques d'usure CDP sur mesure ont été découpées et formées pour s'adapter. Elles ont ensuite été soudées rapidement et facilement au ventilateur. Les joints ont été recouverts d'un rechargement. Après deux ans, aucun signe d'usure n'était apparu, ce qui confirme une augmentation très significative de la durée de vie du ventilateur.
Tamisage et stockage
Les copeaux de taille acceptable doivent être isolés des pièces sous-dimensionnées (fines) et surdimensionnées en faisant passer les copeaux sur une série de tamis. Les copeaux surdimensionnés sont rejetés sur un convoyeur, qui les achemine vers un type de découpeur pour les réduire à une taille plus petite. Ces dernières années, l'épaisseur des copeaux a été reconnue comme une variable importante de la mise en pâte et les tamis modernes à disques ou à rouleaux, qui séparent en fonction de l'épaisseur, sont désormais largement acceptés comme la norme industrielle. Cela signifie que l'usure doit être minimisée afin de maintenir la précision de l'opération de tamisage.
Un séparateur à tamis à copeaux comporte des disques dont les pointes s'usent par l'abrasion des copeaux. Une usure excessive permettrait aux gros copeaux de passer dans le digesteur. Pour rectifier une unité usée, les surfaces des pointes ont été rectifiées et de la poudre a été appliquée par un procédé de projection et fusion. Cette solution a permis d'effectuer une réparation in situ, sans qu'il soit nécessaire de démonter l'unité, de retirer le disque de tamisage et de le remplacer. Des économies importantes ont été réalisées puisque les temps d'arrêt ont été réduits et qu'il n'a pas été nécessaire d'acheter une pièce de rechange.
Mise en pâte
La mise en pâte désigne tout processus par lequel le bois est réduit en une masse fibreuse. Il peut être accompli mécaniquement, thermiquement, chimiquement ou par des combinaisons de ces traitements.
Le coude de décharge des lessiveurs en discontinu est soumis à une corrosion, une érosion, une abrasion, un choc thermique importants dus à la liqueur de cuisson, à la pâte à papier et à la vapeur. Dans un exemple, les zones usées du coude et de la tuyauterie ont été reconstituées avec des électrodes de soudage développées pour les zones soumises à des contraintes critiques. Les faces des brides ont également été recouvertes de manière similaire et usinées jusqu'à la finition. Cela a permis de multiplier par trois la durée de vie de l'usure par rapport à celle du coude d'origine.
Lavage
La pâte cuite provenant des digesteurs doit être lavée pour éliminer la liqueur résiduelle qui contaminerait la pâte lors des étapes de traitement ultérieures et récupérer la quantité maximale de produits chimiques usés avec une dilution minimale.
La corrosion et la fatigue du métal provoquent la rupture et la fissuration des tamis du laveur. Auparavant, ce composant devait être mis au rebut, avec les coûts de démontage et de remplacement associés. En guise d'alternative, l'utilisation d'une baguette de brasure à haute teneur en argent permet une réparation rapide et solide grâce à sa haute résistance à la traction et à sa faible température de liaison.
Blanchiment
Le blanchiment moderne est réalisé par une séquence continue d'étapes de différents processus utilisant des produits chimiques et des conditions différentes à chaque étape, généralement avec un rinçage entre les étapes. Les laveurs et les pompes de l'opération de blanchiment doivent être fabriqués en aciers inoxydables fortement alliés, en alliages de nickel ou en titane. Le contrôle de la corrosion chimique dans l'équipement de blanchiment est un problème permanent.
Un défi particulier est le disque de raffinage qui souffre de fissures dues à la corrosion sous contraintes et d'usure dans la zone de transition entre le disque et le cylindre. Cette zone peut être réparée par sablage puis par projection à l'arc d'un revêtement à base de l'alliage nickel-chrome l’Inconel 625. Le revêtement peut être usiné et rectifié aux dimensions et à la finition de surface requises. Le traitement est rapide à appliquer et réduit les dangers d'une nouvelle fissuration par corrosion sous contraintes, sans provoquer de distorsion du disque.
Traitement
Dans la plupart des processus de fabrication de papier, l’opération de tamisage de la pâte est nécessaire pour éliminer les particules surdimensionnées, gênantes et indésirables des bonnes fibres de fabrication du papier. Les principaux types de tamis de pâte sont les tamis vibrants, les tamis à gravité centrifuge et les tamis à pression (centrifuge ou centripète). Ils ont tous une forme de barrière perforée pour laisser passer les fibres acceptables et rejeter les matières indésirables.
Le traitement complémentaire de la pâte à papier est le raffinage des fibres. Deux grands types de raffineurs continus sont utilisés pour la préparation de la pâte : les raffineurs à disques et les raffineurs coniques.
Le mouvement efficace de la pâte à travers les différentes étapes de traitement est au cœur du fonctionnement d'une usine de pâte et de papier. Aucune usine ne peut fonctionner avec succès sans unités de pompage fiables.
Un défi se trouve sur l'arbre du raffineur, où le manchon en acier inoxydable est usé par le frottement de la douille à collet qui le maintien en place, cette usure est accélérée par la corrosion. Ce problème peut être résolu en projetant sur l'arbre une poudre base Ni refondue au chalumeau, spécialement développé pour résister à la corrosion et réduire la frottement. La durée de vie peut être augmentée de 300% en raison de la dureté supérieure, de la résistance à la corrosion et des propriétés de frottement améliorées du revêtement.
Déchets de papier et de carton
De nombreuses usines utilisent du papier et du carton recyclés en tant que matière première. Certaines usines fonctionnent uniquement avec des matériaux recyclés. Les rebuts sont introduits dans un hydro pulpeur, qui est une cuve verticale avec un rotor rotatif au fond. Le rotor déchiquette le papier et le carton avec de l'eau pour en faire de la pâte et une plaque d'extraction perforée sous le rotor tire les fibres hors de la cuve. Le nettoyage et l'effilochage ultérieurs de la pâte la préparent à la fabrication du papier. Le rotor de l'hydro pulpeur est soumis à une forte usure due aux vieux papiers ainsi qu'à des matériaux étrangers tels que des pierres et de la ferraille.
Dans un cas, il a fallu réparer le rotor au fond de la cuve. La capacité de production diminue considérablement lorsque la roue à aubes est usée. Pour la réparation, les zones critiques ont été protégées par rechargement avec des électrodes développées pour offrir une protection combinée contre l'abrasion, la pression et les impacts modérés. En plus d'augmenter la durée de vie de 2 semaines à 5 mois, le rechargement peut être effectuée trois fois pour réduire davantage les coûts.
Fours à chaux
L'un des principaux défis dans la fabrication de la pâte à papier a toujours été l'entretien et l'efficacité de fonctionnement des fours à chaux dans l'usine de caustification. Il s'agit de grands tubes ronds en acier fabriqués, de 4 à 6 mètres de diamètre, et de 45 à 150 mètres de long. Étant donné qu'ils sont revêtus de briques réfractaires résistantes au feu, qu'ils tournent constamment sur des rouleaux (espacés tous les 5 mètres environ) et qu'ils sont chauffés intérieurement à 1450°C, ils sont susceptibles de connaître de graves problèmes de fonctionnement et de maintenance. Plus le four est long, plus ces problèmes peuvent être importants, notamment en ce qui concerne la fissuration et le désalignement des rouleaux. .
Une réparation réussie a été rendue possible grâce à l'utilisation d'électrodes de soudage à faible température et à une procédure étroitement contrôlée. D'importantes économies ont été réalisées car aucune nouvelle pièce n'a été nécessaire et le temps d'immobilisation a été réduit de 10 à 2 semaines.
La réparation et la remise à neuf donnent souvent de meilleurs résultats que le remplacement
Le premier réflexe des équipes de maintenance dans l'industrie de la pâte et du papier est souvent de remplacer les pièces usées par des articles neufs. Cependant, dans cette industrie, la continuité du fonctionnement est généralement la préoccupation principale. Par conséquent, la réparation et la remise à neuf peuvent s'avérer mieux adaptées dans de nombreux cas. En plus de garantir une remise en service plus rapide, l'utilisation des technologies modernes de revêtement anti-usure améliore de manière significative la durée de vie opérationnelle, souvent de deux à quatre fois. Il en résulte une plus grande fiabilité, une meilleure durabilité et une réduction de coûts de maintenance.